Helpful
Articles
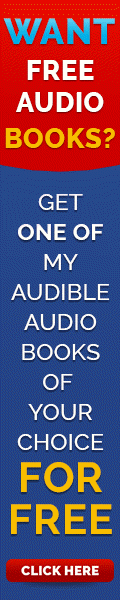
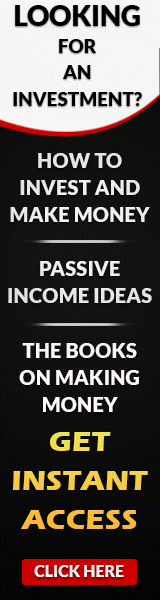
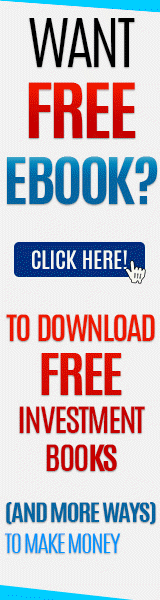
-
Financial
Freedom and Wealth Creation Formula: Discover How to Build
Sustainable Wealth and Become Financially Free
-
Poverty: So,
You Want to Remain Financially Poor? Great
Ways to Become Financially Poor and Remain Poor
-
Want
to Start a Business Career Online? The Essential Things You Need
To Know Before You Start a Money Making Internet Business
-
Immigrants
and the Most Popular Jobs: Seasonal Work, Skilled, Unskilled and
Highly-Skilled Jobs Opportunities in the United States of
America for Foreigners or Immigrants (Top
Jobs Among All Immigrants In The United States Of America)
-
A
Healthier Choice: Quick and Ridiculously Easy Ways to Get
Active, Get Healthier, Feel Great, Look Better, Improve Your
Overall Health and Wellbeing Fast (Health & Well-Being Tips)
-
Want
To Retire Early? How To Plan For Retirement - Here Are The Steps
To Take If You Want To Retire Early (Essential Tips and Tricks)
-
Genuine
Ways To Make Money: Here Are Some Business Ideas To Get You
Started (Surprisingly Easy Methods To Make Money)
-
Looking
For Great Investment Ideas To Make Money? Here Are Some Smart,
Profitable and Lucrative Business Investment Ideas You Can
Launch for Cheap
-
How
To Get More Traffic to My Website? Effective Ways to Instantly
Get High Quality Web Traffic to Your Website or Blog and Make
More Money Online - (Website Traffic Tips)
-
Craigslist
Money Making Opportunities: A Creative Guide to Successfully
Make a Full-Time Income Selling on Craigslist (Tips to Make
Money on Craigslist)
-
Affiliate
Marketing Sales: Make Multiple Streams of Income with Affiliate
Marketing (Work at Home Jobs - Get More Traffic and Sales With
Affiliate Marketing)
-
Money
Management: Simple Tips to Reach Financial Freedom - Beginners
Guide to Saving Money, Living a Debt Free Life and Retire a
Millionaire
-
Legitimate
Work From Home Job
Opportunities For Stay at Home Moms and Dads That
Are Easy to Start (Unique Side Hustles Business Ideas and Great
Second Jobs For Extra Money)
-
The
Most Lucrative and Proven Side Hustles Business Ideas for
Medical Professionals, Attorneys or Lawyers and Accountants
& Auditors
-
Skilled,
Unskilled and Highly-Skilled Immigrants Jobs in the United
Kingdom: Britain's
Most In-Demand Immigrants Jobs Revealed -
High Demand Jobs For Foreigners In The United Kingdom (Jobs In
The United Kingdom For Foreigners or Immigrants)
-
Gold’s
Role As Money: Gold Standard Perspective On Financial Systems
And The World’s Economy - The Most Perfect Monetary System –
(The Gold Standard is a Better Monetary System)
-
Why
Invest In Nigeria? Reasons Why You Should Invest In The Nigerian
Economy – (Best Investment And Business Opportunities In
Nigeria)
-
The
Ultimate Pinterest Strategies: Pinterest Strategies to Quickly
Grow and Drive Huge Traffic To Your Website or Blog - Make
Pinterest Work For Your Business (Pinterest
Marketing Tips and Strategies)
-
How
To Run a Successful Email Marketing Campaign: Using Email To
Promote and Grow Your Business - (Must Have Tips To Create a
Successful and Effective Email Marketing Strategies)
-
Vlogging
On YouTube: How To Make Money Online Through Vlogging On YouTube
- (Tips
To Get Started Making Money Vlogging)
-
Experience
African Vacations: The Most Amazing and Popular Travel
Destinations to Visit in Africa (Tourist Attractions in Africa)
-
Where
To Invest In Africa? The Top 6 Most Attractive African Countries
To Invest Your Money And Reasons To Invest In Africa - (African
Countries With Good Investment Potentials)
-
The
Most Attractive Countries In Asia To Invest Your Money -
Investment Opportunities in Asia
-
Getting
to Know…The Kitchen Porters - KP for Short (Diary of an
Immigrant or Foreigner as a Kitchen Porter or Kitchen Steward in
the United Kingdom)
-
Investment
Opportunities in Africa: How You Can Build Sustainable Wealth
Investing in Africa (Ways
to Build Wealth in Africa)
-
Offshore
Investment Opportunities: Most Attractive Offshore Locations To
Invest Your Money (The World's Top Offshore Countries To Put
Your Money)
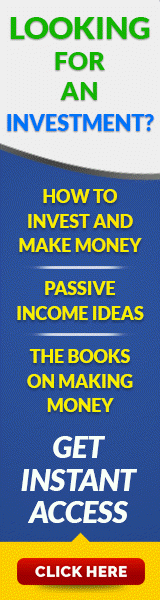
|
Comprehensive
Guide on How to Start a Wood Chip Manufacturing Business
Chapter 1: Introduction
Overview of the wood chip manufacturing industry
Importance of wood chips in various sectors
Potential market opportunities
Chapter 2: Market Research and Analysis
Conducting market research to identify target customers
Analyzing the demand and supply trends in the wood chip industry
Evaluating potential competitors
Chapter 3: Business Plan Development
Defining the vision, mission, and goals of your wood chip manufacturing business
Outlining the business structure and legal requirements
Creating a comprehensive business plan
Chapter 4: Financing Your Business
Estimating the startup costs and capital requirements
Exploring funding options, such as loans, investors, or grants
Developing a financial strategy for your wood chip manufacturing business
Chapter 5: Location and Facilities
Selecting a suitable location for your manufacturing plant
Assessing the space and infrastructure requirements
Considering environmental regulations and permits
Chapter 6: Procuring Equipment and Machinery
Identifying the necessary machinery and equipment for wood chip production
Evaluating suppliers and obtaining price quotations
Purchasing or leasing equipment based on your budget and production needs
Chapter 7: Raw Material Procurement
Identifying sources of wood for chipping
Establishing relationships with timber suppliers or logging companies
Ensuring a steady supply of quality raw materials
Chapter 8: Production Process
Understanding the wood chipping process
Developing a standardized production workflow
Ensuring efficient and safe manufacturing practices
Chapter 9: Quality Control and Assurance
Implementing quality control measures for wood chips
Setting up a quality assurance program to maintain consistent product standards
Testing and monitoring the moisture content, size, and cleanliness of wood chips
Chapter 10: Packaging and Distribution
Selecting appropriate packaging materials for wood chips
Designing a branding and labeling strategy
Establishing distribution channels to reach customers efficiently
Chapter 11: Marketing and Sales
Developing a marketing plan to promote your wood chips
Identifying target industries and customers
Implementing advertising, online marketing, and sales strategies
Chapter 12: Building Customer Relationships
Providing excellent customer service
Establishing long-term relationships with key customers
Seeking feedback and continuously improving your products and services
Chapter 13: Environmental Considerations
Ensuring sustainable wood sourcing practices
Implementing waste management and recycling initiatives
Complying with environmental regulations and certifications
Chapter 14: Hiring and Managing Employees
Identifying the required workforce and skill sets
Developing job descriptions and conducting recruitment
Establishing employee training programs and performance evaluation systems
Chapter 15: Legal and Regulatory Compliance
Understanding the legal and regulatory requirements of operating a wood chip manufacturing business
Obtaining necessary licenses, permits, and certifications
Complying with safety, labor, and environmental regulations
Chapter 16: Insurance and Risk Management
Assessing potential risks and developing risk management strategies
Obtaining suitable insurance coverage for your business
Establishing safety protocols to minimize accidents and liabilities
Chapter 17: Financial Management
Establishing accounting systems and record-keeping practices
Managing cash flow, expenses, and revenue
Implementing cost control measures to maximize profitability
Chapter 18: Scaling and Growth Strategies
Identifying opportunities for expansion and growth
Developing strategies to enter new markets or expand product offerings
Evaluating potential partnerships or acquisitions
Chapter 19: Technology and Innovation
Exploring technological advancements in wood chip manufacturing
Implementing automation and digital solutions to improve efficiency
Monitoring industry trends and adapting to changes
Chapter 20: Risk Assessment and Contingency Planning
Conducting risk assessments and contingency planning for potential disruptions
Developing backup plans for equipment failure, supply chain interruptions, or market fluctuations
Establishing a crisis management protocol
Chapter 21: Long-Term Sustainability
Considering long-term sustainability and business continuity
Evaluating renewable energy options for the manufacturing process
Engaging in responsible forest management practices
Chapter 22: Networking and Industry Engagement
Joining industry associations and trade organizations
Participating in conferences, exhibitions, and workshops
Networking with industry professionals and potential partners
Chapter 23: Monitoring and Evaluation
Setting key performance indicators (KPIs) for your wood chip manufacturing business
Regularly reviewing and evaluating business performance
Making necessary adjustments and improvements
Chapter 24: Challenges and Lessons Learned
Identifying common challenges in the wood chip manufacturing industry
Sharing lessons learned from experienced business owners
Providing tips and strategies to overcome obstacles
Chapter 25: Conclusion and Future Outlook
Summarizing the key points discussed in the article
Highlighting the potential future trends and opportunities in the wood chip manufacturing industry
Encouraging readers to take action and start their own wood chip manufacturing business
Chapter 1: Introduction
Wood chip manufacturing is a thriving industry that plays a vital role in various sectors, including agriculture, forestry, energy, and
construction. Wood chips are small pieces of wood obtained by chipping or shredding larger logs or timber. These chips serve as a versatile raw material used in applications such as fuel for biomass power plants, animal bedding, landscaping mulch, paper production, and composite materials.
1.1 Overview of the wood chip manufacturing industry:
The wood chip manufacturing industry has witnessed significant growth in recent years due to the increased demand for renewable energy sources, sustainable packaging materials, and environmentally friendly products. This growth has been driven by factors such as the rising awareness of climate change, government initiatives promoting renewable energy, and the need for eco-friendly alternatives to traditional materials.
1.2 Importance of wood chips in various sectors:
Wood chips have diverse applications across different sectors. In the energy sector, they are used as a biomass fuel for generating heat and electricity, reducing dependence on fossil fuels. In the agricultural sector, wood chips serve as animal bedding material, providing a comfortable and hygienic environment for livestock. They are also used in horticulture and landscaping as mulch, improving soil health, moisture retention, and weed suppression. Additionally, wood chips are utilized in the production of paper and composite materials, contributing to the sustainability of these industries.
1.3 Potential market opportunities:
The wood chip manufacturing business offers numerous market opportunities. The demand for renewable energy sources is expected to grow, creating a constant need for wood chips as biomass fuel. With the increasing focus on sustainable packaging, there is a rising demand for wood chips for the production of paper and eco-friendly packaging materials. The agricultural and landscaping sectors also present significant opportunities for the supply of wood chips as animal bedding and mulch. By identifying specific market segments and establishing strategic partnerships, entrepreneurs can tap into these opportunities and build a successful wood chip manufacturing business.
Chapter 2: Market Research and Analysis
2.1 Conducting market research to identify target customers:
Thorough market research is essential to understand the demand and potential customers for wood chips. This includes analyzing the current and projected market size, identifying key industry players, and evaluating customer preferences and requirements. Conducting surveys, interviews, and focus groups can provide valuable insights into the needs, challenges, and purchasing behavior of potential customers.
2.2 Analyzing the demand and supply trends in the wood chip industry:
Examining demand and supply trends helps in assessing market dynamics, pricing fluctuations, and supply chain challenges. It involves studying factors such as the growth rate of biomass power plants, government policies, environmental regulations, and the availability of raw materials. By understanding these trends, entrepreneurs can make informed decisions regarding production capacity, pricing strategies, and market entry timing.
2.3 Evaluating potential competitors:
Identifying and analyzing competitors is crucial for positioning your wood chip manufacturing business in the market. This includes researching existing wood chip manufacturers, their product offerings, pricing strategies, distribution channels, and customer base. Understanding the strengths and weaknesses of competitors can help in developing unique selling propositions and differentiation strategies for your business.
Chapter 3: Business Plan Development
3.1 Defining the vision, mission, and goals of your wood chip manufacturing business:
Developing a clear vision, mission, and set of goals is the foundation of a successful wood chip manufacturing business. The vision outlines the long-term aspirations of the company, while the mission defines its purpose and core values. Setting specific and measurable goals provides a roadmap for growth and helps in monitoring progress.
3.2 Outlining the business structure and legal requirements:
Choosing the appropriate legal structure for your wood chip manufacturing business, such as sole proprietorship, partnership, or limited liability company, is crucial for legal and financial reasons. Researching and complying with local and national regulations, permits, licenses, and environmental standards is essential to ensure legal and operational compliance.
3.3 Creating a comprehensive business plan:
A well-crafted business plan serves as a roadmap for your wood chip manufacturing business. It should include an executive summary, company description, market analysis, organization and management structure, product line description, marketing and sales strategies, financial projections, and risk assessment. A comprehensive business plan increases your chances of securing funding, attracts potential investors, and guides your business operations.
Chapter 4: Financing Your Business
4.1 Estimating the startup costs and capital requirements:
Determining the initial investment required to start your wood chip manufacturing business is crucial for securing financing. Start-up costs may include the purchase or lease of land, machinery and equipment, raw materials, permits and licenses, marketing expenses, and working capital. Conducting a detailed cost analysis and budgeting process helps in estimating the required capital and identifying potential funding sources.
4.2 Exploring funding options, such as loans, investors, or grants:
There are various funding options available to finance your wood chip manufacturing business. Traditional bank loans, Small Business Administration (SBA) loans, and lines of credit can provide necessary capital. Alternatively, attracting investors who believe in your business concept and growth potential can bring in additional funds in exchange for equity or debt. Additionally, government grants, subsidies, or crowdfunding platforms can be explored as potential sources of financing.
4.3 Developing a financial strategy for your wood chip manufacturing business:
Creating a financial strategy is essential for managing cash flow, tracking expenses, and projecting revenues. This includes developing financial statements, such as income statements, balance sheets, and cash flow statements. Implementing an accounting system and seeking professional advice from accountants or financial consultants can help ensure accurate financial management and reporting.
Chapter 5: Location and Facilities
5.1 Selecting a suitable location for your manufacturing plant:
Choosing the right location is crucial for the success of your wood chip manufacturing business. Factors to consider include proximity to raw material sources, accessibility to transportation networks, availability of utilities, and zoning regulations. Assessing local market demand and competition can also influence your decision on the optimal location.
5.2 Assessing the space and infrastructure requirements:
Determining the space and infrastructure requirements for your manufacturing plant is essential for efficient operations. This includes the size of the production facility, storage areas for raw materials and finished products, office space, employee facilities, and parking. Collaborating with architects, engineers, and contractors can help in designing and optimizing the layout of your facility.
5.3 Considering environmental regulations and permits:
Compliance with environmental regulations is crucial for sustainable and responsible wood chip manufacturing. Assessing and adhering to air and water quality standards, noise regulations, waste management guidelines, and forestry practices is necessary. Obtaining the required permits and certifications from local environmental authorities demonstrates your commitment to sustainability and helps build trust with customers and stakeholders.
Chapter 6: Procuring Equipment and Machinery
6.1 Identifying the necessary machinery and equipment for wood chip production:
Selecting the appropriate machinery and equipment is vital for efficient and high-quality wood chip manufacturing. This includes chippers, grinders, shredders, screening equipment, conveyors, drying systems, and storage containers. Researching reputable suppliers, comparing equipment specifications, and considering factors such as production capacity, energy efficiency, and maintenance requirements are essential for making informed purchasing decisions.
6.2 Evaluating suppliers and obtaining price quotations:
Evaluating potential equipment suppliers is crucial for ensuring quality, reliability, and ongoing technical support. Requesting price quotations from multiple suppliers helps in comparing costs, warranties, and after-sales service. Considering factors such as reputation, customer reviews, and the supplier's track record in the industry enhances the likelihood of obtaining reliable machinery and equipment.
6.3 Purchasing or leasing equipment based on your budget and production needs:
Deciding whether to purchase or lease equipment depends on your budget, production volume, and long-term business goals. Purchasing equipment provides ownership and control but requires a larger upfront investment. Leasing equipment can provide flexibility, lower initial costs, and potential tax advantages. Analyzing the financial implications and consulting with equipment finance specialists can help in making the best decision for your wood chip manufacturing business.
Chapter 7: Raw Material Procurement
7.1 Identifying sources of wood for chipping:
Securing a consistent and reliable supply of raw materials is essential for uninterrupted wood chip production. Establishing relationships with timber suppliers, logging companies, sawmills, or forestry operations is crucial. Exploring local and regional sources helps in minimizing transportation costs and ensuring a sustainable supply chain.
7.2 Establishing relationships with timber suppliers or logging companies:
Building strong relationships with timber suppliers or logging companies is beneficial for your wood chip manufacturing business. Engaging in open and transparent communication, negotiating favorable terms, and ensuring a consistent supply of quality logs are key considerations. Long-term contracts or partnerships can provide stability and help in securing competitive pricing for raw materials.
7.3 Ensuring a steady supply of quality raw materials:
Ensuring the quality of raw materials is critical for producing high-quality wood chips. Implementing quality control measures, such as specifying size and moisture content requirements, conducting regular inspections, and monitoring the harvesting and transportation processes, helps in maintaining consistent product standards. Building strong relationships with suppliers and maintaining open lines of communication contribute to a reliable and steady supply of raw materials.
Chapter 8: Production Process
8.1 Understanding the wood chipping process:
Understanding the wood chipping process is fundamental for efficient and productive operations. The process involves feeding logs into chippers or grinders, where they are cut or shredded into small wood chips. Depending on the desired end product, additional steps such as screening, drying, or further processing may be required. Implementing best practices, optimizing machinery settings, and training employees on safety protocols enhance productivity and product quality.
8.2 Developing a standardized production workflow:
Developing a standardized production workflow helps streamline operations and maximize efficiency. This includes establishing clear procedures for equipment setup and maintenance, raw material handling, chipping processes, quality control checks, and packaging. Creating standard operating procedures (SOPs) and providing comprehensive training to employees ensures consistency, reduces errors, and increases overall productivity.
8.3 Ensuring efficient and safe manufacturing practices:
Efficiency and safety are paramount in wood chip manufacturing. Regular equipment maintenance, routine inspections, and adherence to safety protocols minimize the risk of accidents and ensure a safe working environment. Implementing safety training programs, providing personal protective equipment (PPE), and fostering a culture of safety awareness among employees are vital for a successful and sustainable manufacturing operation.
Chapter 9: Quality Control and Assurance
9.1 Implementing quality control measures for wood chips:
Maintaining consistent product quality is essential for customer satisfaction and building a reputable brand. Implementing quality control measures involves establishing specifications for chip size, moisture content, cleanliness, and other relevant characteristics. Conducting regular quality checks throughout the production process, utilizing advanced testing methods, and documenting quality control procedures ensure the delivery of high-quality wood chips.
9.2 Setting up a quality assurance program to maintain consistent product standards:
Implementing a comprehensive quality assurance program is crucial for consistent product standards. This involves establishing quality control checkpoints, conducting regular inspections and tests, and documenting the results. Continuous monitoring and analysis of quality data help identify areas for improvement, optimize production processes, and meet customer expectations consistently.
9.3 Testing and monitoring the moisture content, size, and cleanliness of wood chips:
Moisture content, size, and cleanliness are critical parameters for wood chips, as they affect their performance in various applications. Implementing moisture content testing methods, such as oven drying or moisture meters, ensures compliance with industry standards. Regularly monitoring chip size and cleanliness through sieving and visual inspections guarantees consistent product quality. Implementing automated systems or manual checks at different stages of the production process helps in identifying and addressing any deviations from quality standards.
Chapter 10: Packaging and Distribution
10.1 Selecting appropriate packaging materials for wood chips:
Choosing the right packaging materials is essential for preserving the quality and ensuring the safe transportation of wood chips. Factors such as moisture resistance, durability, and environmental considerations should be taken into account. Packaging options may include bags, bulk containers, or customized packaging solutions. Conducting packaging trials, considering customer preferences, and complying with packaging regulations contribute to efficient and attractive packaging.
10.2 Designing a branding and labeling strategy:
Developing a strong branding and labeling strategy helps differentiate your wood chips in the market. Designing a visually appealing logo, choosing appropriate packaging colors and graphics, and creating a compelling brand story contribute to brand recognition and customer loyalty. Additionally, complying with labeling requirements, such as providing product information, certifications, and safety instructions, enhances transparency and builds trust with customers.
10.3 Establishing distribution channels to reach customers efficiently:
Establishing efficient distribution channels is crucial for timely delivery and customer satisfaction. Identifying potential customers and target markets helps determine the most appropriate distribution channels. These may include direct sales to end-users, partnerships with distributors or retailers, or online sales platforms. Developing strong relationships with logistics providers and optimizing transportation routes and logistics operations contribute to timely and cost-effective product distribution.
Chapter 11: Marketing and Sales
11.1 Developing a marketing plan to promote your wood chips:
Creating a comprehensive marketing plan is essential for promoting your wood chips and generating demand. This includes defining your target market segments, conducting market research, and identifying key marketing channels. Developing a compelling value proposition, positioning your brand effectively, and implementing marketing strategies such as advertising, public relations, digital marketing, and trade shows help in reaching and attracting potential customers.
11.2 Identifying target industries and customers:
Identifying target industries and customers helps focus your marketing efforts and tailor your product offerings to specific needs. Wood chips find applications in industries such as biomass energy, agriculture, horticulture, paper production, and construction. Understanding the unique requirements, preferences, and pain points of these industries allows you to develop targeted marketing messages and build strong customer relationships.
11.3 Implementing advertising, online marketing, and sales strategies:
Implementing advertising, online marketing, and sales strategies helps promote your wood chips effectively. This includes creating a professional website with detailed product information, utilizing search engine optimization (SEO) techniques to improve online visibility, engaging in content marketing through blogs or social media, and leveraging digital advertising platforms. Additionally, developing a sales strategy that includes effective lead generation, nurturing customer relationships, and providing exceptional customer service contributes to sales growth and customer loyalty.
Chapter 12: Building Customer Relationships
12.1 Providing excellent customer service:
Delivering excellent customer service is crucial for building long-term relationships and fostering customer loyalty. This includes timely and responsive communication, addressing customer inquiries or concerns promptly, and providing after-sales support. Implementing customer feedback mechanisms and continually improving your products and services based on customer input demonstrates your commitment to meeting customer needs and exceeding their expectations.
12.2 Establishing long-term relationships with key customers:
Nurturing long-term relationships with key customers is beneficial for stable and recurring business. This involves understanding their specific requirements, providing personalized solutions, and building trust and reliability through consistent product quality and on-time deliveries. Regular communication, conducting business reviews, and seeking opportunities for collaboration or value-added services help strengthen customer relationships and foster loyalty.
12.3 Seeking feedback and continuously improving your products and services:
Customer feedback is invaluable for identifying areas of improvement and enhancing your products and services. Encouraging customers to provide feedback through surveys, interviews, or online reviews helps you understand their satisfaction levels, preferences, and expectations. Analyzing feedback, implementing necessary changes, and communicating improvements to customers demonstrate your commitment to continuous improvement and customer-centricity.
Chapter 13: Environmental Considerations
13.1 Ensuring sustainable wood sourcing practices:
Sustainable wood sourcing is essential for the long-term viability of your wood chip manufacturing business. Implementing responsible forestry practices, such as replanting or supporting certified sustainable forestry programs, contributes to environmental conservation. Collaborating with suppliers who adhere to sustainable forestry standards, such as Forest Stewardship Council (FSC) certification, demonstrates your commitment to environmental sustainability and attracts environmentally conscious customers.
13.2 Implementing waste management and recycling initiatives:
Wood chip manufacturing processes generate waste materials that can be managed and recycled effectively. Implementing waste management strategies, such as recycling wood scraps or using them for other value-added products, helps minimize waste and reduce environmental impact. Additionally, complying with waste disposal regulations, promoting recycling among customers, and exploring partnerships with recycling facilities contribute to a circular economy approach.
13.3 Complying with environmental regulations and certifications:
Compliance with environmental regulations and obtaining relevant certifications is vital for operating your wood chip manufacturing business responsibly. This includes understanding and adhering to air and water quality standards, noise regulations, and waste management guidelines. Obtaining certifications such as ISO 14001 (Environmental Management System) or other recognized eco-labels reinforces your commitment to environmental stewardship and differentiates your business in the market.
Chapter 14: Hiring and Managing Employees
14.1 Identifying the required workforce and skill sets:
Identifying the required workforce and skill sets is crucial for smooth operations and maintaining production efficiency. Roles may include machine operators, maintenance technicians, quality control personnel, administrative staff, and sales and marketing professionals. Assessing the specific skills and experience needed for each role and creating job descriptions help in recruiting the right talent.
14.2 Developing job descriptions and conducting recruitment:
Developing clear and detailed job descriptions helps attract qualified candidates who align with your business needs. Conducting recruitment through various channels, such as online job portals, industry networks, or partnerships with vocational schools or universities, widens the talent pool. Implementing a rigorous recruitment process, including interviews, assessments, and reference checks, ensures the selection of competent and dedicated employees.
14.3 Establishing employee training programs and performance evaluation systems:
Investing in employee training programs is essential for developing a skilled workforce and enhancing productivity. Providing initial training on equipment operation, safety protocols, and quality control procedures ensures that employees have the necessary knowledge and skills. Implementing ongoing training and development initiatives, performance evaluations, and recognition programs contribute to employee motivation, satisfaction, and retention.
Chapter 15: Legal and Regulatory Compliance
15.1 Understanding the legal and regulatory requirements of operating a wood chip manufacturing business:
Complying with legal and regulatory requirements is crucial for operating your wood chip manufacturing business ethically and responsibly. Familiarize yourself with local, national, and international laws and regulations related to manufacturing, environmental protection, labor, safety, and product quality. Engaging legal counsel and staying updated with industry-specific regulations help ensure compliance and mitigate legal risks.
15.2 Obtaining necessary licenses, permits, and certifications:
Obtaining the necessary licenses, permits, and certifications is a legal requirement for operating a wood chip manufacturing business. This may include business licenses, environmental permits, health and safety certifications, and any specific certifications required for international trade. Researching and understanding the application processes, fees, and renewal requirements ensures that your business operates within the legal framework.
15.3 Complying with safety, labor, and environmental regulations:
Prioritizing safety, labor rights, and environmental sustainability is essential for ethical and responsible business operations. Establishing safety protocols, providing appropriate safety training, and conducting regular inspections help create a safe work environment. Complying with labor laws, such as fair wages and working hours, and promoting a respectful and inclusive workplace culture contribute to employee satisfaction and productivity. Adhering to environmental regulations and implementing sustainable practices demonstrate your commitment to minimizing environmental impact.
Chapter 16: Insurance and Risk Management
16.1 Assessing potential risks and developing risk management strategies:
Identifying potential risks and developing risk management strategies is essential for protecting your wood chip manufacturing business. Conducting a thorough risk assessment helps identify areas of vulnerability, such as equipment breakdowns, supply chain disruptions, or natural disasters. Developing risk mitigation strategies, contingency plans, and business continuity plans minimize the impact of unforeseen events and ensure the resilience of your operations.
16.2 Obtaining suitable insurance coverage for your business:
Insurance coverage is vital for mitigating financial risks and protecting your wood chip manufacturing business from potential liabilities. Consult with insurance professionals who specialize in the manufacturing industry to determine the appropriate coverage, such as general liability insurance, property insurance, workers' compensation insurance, and product liability insurance. Reviewing and updating insurance policies regularly ensures that your coverage aligns with the evolving needs of your business.
16.3 Establishing safety protocols to minimize accidents and liabilities:
Implementing robust safety protocols is crucial for preventing accidents, ensuring employee well-being, and minimizing liabilities. This includes providing proper training on equipment operation and safety procedures, conducting regular safety inspections, and promoting a safety-conscious culture among employees. Maintaining detailed records of safety training, incidents, and corrective actions helps in monitoring and improving safety performance.
Chapter 17: Financial Management
17.1 Establishing accounting systems and record-keeping practices:
Implementing effective accounting systems and record-keeping practices is crucial for accurate financial management. Utilizing accounting software or engaging professional accountants helps in organizing financial data, generating financial statements, tracking expenses, and managing invoices and payments. Regularly reconciling accounts, keeping detailed records, and maintaining a centralized financial database contribute to efficient financial management and compliance with tax regulations.
17.2 Managing cash flow, expenses, and revenue:
Managing cash flow is essential for the smooth operation of your wood chip manufacturing business. This includes accurately forecasting cash inflows and outflows, monitoring and optimizing working capital, and implementing effective invoicing and payment collection processes. Tracking expenses, controlling costs, and analyzing revenue trends help in identifying opportunities for cost savings and revenue growth.
17.3 Implementing cost control measures to maximize profitability:
Implementing cost control measures is crucial for maximizing profitability in the wood chip manufacturing business. This includes regularly reviewing and optimizing operational costs, such as raw material procurement, energy consumption, equipment maintenance, and labor expenses. Negotiating favorable terms with suppliers, implementing lean manufacturing principles, and exploring opportunities for process automation or efficiency improvements contribute to cost reduction and increased profitability.
Chapter 18: Scaling and Growth Strategies
18.1 Identifying opportunities for expansion and growth:
Identifying opportunities for expansion and growth is crucial for the long-term success of your wood chip manufacturing business. This may involve diversifying your product offerings, expanding into new geographic markets, or targeting new customer segments. Conducting market research, analyzing industry trends, and seeking feedback from customers and industry experts help in identifying potential growth opportunities.
18.2 Developing strategies to enter new markets or expand product offerings:
Developing strategies to enter new markets or expand product offerings requires a thorough understanding of customer needs and market dynamics. This may involve conducting market research in the target market, adapting products to meet local preferences, establishing distribution networks, and building partnerships with local businesses or distributors. Implementing effective marketing and promotional strategies tailored to the new market contributes to successful market entry and expansion.
18.3 Evaluating potential partnerships or acquisitions:
Partnerships or acquisitions can be strategic approaches to accelerate growth and expand your wood chip manufacturing business. This may involve collaborating with complementary businesses, such as timber suppliers or wood product manufacturers, to create synergies and access new markets. Conducting due diligence, assessing financial and operational compatibility, and negotiating favorable partnership or acquisition terms contribute to successful collaborations.
Chapter 19: Technology and Innovation
19.1 Exploring technological advancements in wood chip manufacturing:
Keeping up with technological advancements in wood chip manufacturing is crucial for maintaining competitiveness and operational efficiency. Researching and adopting innovative technologies, such as advanced chipping equipment, automated sorting and screening systems, or real-time monitoring and control systems, can enhance productivity, product quality, and cost-effectiveness. Engaging with industry associations and attending trade shows or conferences can provide insights into emerging technologies.
19.2 Implementing automation and digital solutions to improve efficiency:
Automation and digital solutions can streamline processes and improve efficiency in wood chip manufacturing. This may include implementing automated equipment control systems, integrating inventory management and production planning software, or utilizing data analytics for predictive maintenance and process optimization. Assessing the cost-effectiveness and ROI of implementing automation and digital solutions is essential in determining the optimal technologies for your business.
19.3 Monitoring industry trends and adapting to changes:
Staying informed about industry trends and emerging market demands is essential for staying competitive in the wood chip manufacturing industry. Monitoring market reports, industry publications, and attending industry events help in understanding evolving customer preferences, regulatory changes, and technological advancements. Being adaptable and proactive in embracing new trends and technologies positions your business for long-term success.
Chapter 20: Risk Assessment and Contingency Planning
20.1 Conducting risk assessments and contingency planning for potential disruptions:
Identifying and assessing potential risks and disruptions is essential for developing effective contingency plans. This includes analyzing risks such as equipment failure, supply chain interruptions, natural disasters, or market fluctuations. Creating contingency plans that outline alternative sourcing options, backup equipment arrangements, and crisis management protocols ensures business continuity and minimizes the impact of unforeseen events.
20.2 Developing backup plans for equipment failure, supply chain interruptions, or market fluctuations:
Having backup plans in place for potential disruptions helps mitigate the impact on your wood chip manufacturing business. This may involve maintaining spare parts and backup equipment, establishing alternative supply sources or contracts with multiple suppliers, or diversifying customer base to reduce dependency on specific market segments. Regularly reviewing and updating backup plans based on changing circumstances and risks helps ensure preparedness for potential disruptions.
Chapter 21: Long-Term Sustainability
21.1 Considering long-term sustainability and business continuity:
Long-term sustainability is crucial for the success and longevity of your wood chip manufacturing business. This involves considering factors such as resource management, environmental impact, community engagement, and social responsibility. Implementing sustainable practices, monitoring and reducing carbon footprint, and contributing to the local economy through job creation and community initiatives contribute to long-term business viability.
21.2 Evaluating renewable energy options for the manufacturing process:
Exploring renewable energy options for powering your manufacturing process aligns with sustainability goals. This may include investing in renewable energy sources such as solar panels, biomass boilers, or cogeneration systems. Conducting feasibility studies, assessing cost-effectiveness, and leveraging government incentives or grants can support the transition to renewable energy, reduce reliance on fossil fuels, and lower operational costs.
21.3 Engaging in responsible forest management practices:
Responsible forest management is crucial for the sustainable sourcing of wood materials. This involves adhering to recognized forestry standards, supporting reforestation efforts, and promoting biodiversity conservation. Partnering with certified forest management organizations, obtaining sustainable forest certifications, and actively participating in sustainable forestry initiatives contribute to the preservation and long-term health of forests.
Chapter 22: Networking and Industry Engagement
22.1 Joining industry associations and trade organizations:
Becoming a member of industry associations and trade organizations provides numerous benefits to your wood chip manufacturing business. These associations offer networking opportunities, industry insights, and access to resources and training programs. Participation in conferences, workshops, and seminars organized by these associations enhances industry knowledge, facilitates collaboration, and strengthens your position within the industry.
22.2 Participating in conferences, exhibitions, and workshops:
Attending and participating in conferences, exhibitions, and workshops related to wood chip manufacturing provides valuable opportunities to showcase your products, network with industry professionals, and stay updated on the latest industry trends. These events offer a platform for knowledge sharing, market intelligence, and establishing business relationships with potential customers, suppliers, and partners.
22.3 Networking with industry professionals and potential partners:
Building a strong network of industry professionals and potential partners is invaluable for your wood chip manufacturing business. Engaging in networking events, industry forums, and online communities allows you to connect with individuals who can provide valuable insights, collaborations, and business opportunities. Networking helps broaden your reach, gain industry visibility, and stay connected with industry developments.
Chapter 23: Monitoring and Evaluation
23.1 Setting key performance indicators (KPIs) for your wood chip manufacturing business:
Setting key performance indicators (KPIs) is crucial for monitoring and evaluating the performance of your wood chip manufacturing business. KPIs may include production volume, product quality, customer satisfaction, revenue growth, and cost efficiency. Establishing measurable targets and regularly tracking and analyzing KPIs helps in identifying areas of improvement, making informed decisions, and ensuring business success.
23.2 Regularly reviewing and evaluating business performance:
Regularly reviewing and evaluating your wood chip manufacturing business's performance is essential for continuous improvement. Conducting periodic assessments of financial performance, operational efficiency, customer feedback, and market trends allows you to identify strengths, weaknesses, opportunities, and threats. Regular performance reviews enable data-driven decision-making, strategic adjustments, and the implementation of improvement initiatives.
23.3 Making necessary adjustments and improvements:
Based on the insights gained from performance evaluations, it is important to make necessary adjustments and improvements to enhance the success of your wood chip manufacturing business. This may involve refining operational processes, updating marketing strategies, optimizing supply chain management, or investing in new technologies. Embracing a culture of continuous improvement ensures your business remains competitive and adaptable to changing market conditions.
Chapter 24: Challenges and Lessons Learned
24.1 Identifying common challenges in the wood chip manufacturing industry:
The wood chip manufacturing industry faces various challenges that entrepreneurs should be prepared to address. These challenges may include fluctuations in raw material availability and pricing, market volatility, regulatory changes, intense competition, and technological advancements. Understanding these challenges helps in developing contingency plans, fostering resilience, and proactively seeking solutions to mitigate potential risks.
24.2 Sharing lessons learned from experienced business owners:
Learning from the experiences of seasoned business owners in the wood chip manufacturing industry can provide valuable insights and guidance. Seeking mentorship or engaging in industry networks allows you to benefit from the knowledge and lessons learned by those who have navigated similar challenges. Gaining insights into best practices, avoiding common pitfalls, and accessing industry-specific expertise accelerates your learning curve and increases the likelihood of success.
24.3 Providing tips and strategies to overcome obstacles:
To overcome challenges in the wood chip manufacturing industry, it is important to implement effective strategies and leverage industry-specific tips. Strategies may include diversifying your customer base, establishing strong supplier relationships, investing in research and development to differentiate your products, and staying updated on market trends. Adapting to changing customer demands, prioritizing innovation, and fostering a culture of agility and resilience contribute to overcoming obstacles and maintaining a competitive edge.
Chapter 25: Conclusion and Future Outlook
25.1 Summarizing the key points discussed in the article:
In conclusion, starting a wood chip manufacturing business requires careful planning, market research, and adherence to legal and regulatory requirements. Understanding customer needs, ensuring a sustainable supply chain, maintaining product quality, and implementing effective marketing and sales strategies are critical for success.
25.2 Highlighting the potential future trends and opportunities in the wood chip manufacturing industry:
The wood chip manufacturing industry is expected to continue growing in the future due to increasing demand for renewable energy sources, sustainable materials, and eco-friendly solutions. Future trends may include advancements in technology, such as smart manufacturing and automation, as well as the emergence of new markets and applications for wood chips. Embracing sustainability, innovation, and strategic partnerships can position your business for long-term success in this evolving industry.
25.3 Encouraging readers to take action and start their own wood chip manufacturing business:
The wood chip manufacturing industry offers significant opportunities for entrepreneurs willing to invest in a sustainable and innovative business. By following the steps outlined in this comprehensive guide, conducting thorough research, and developing a solid business plan, aspiring business owners can embark on a rewarding journey in the wood chip manufacturing sector.
Featured books
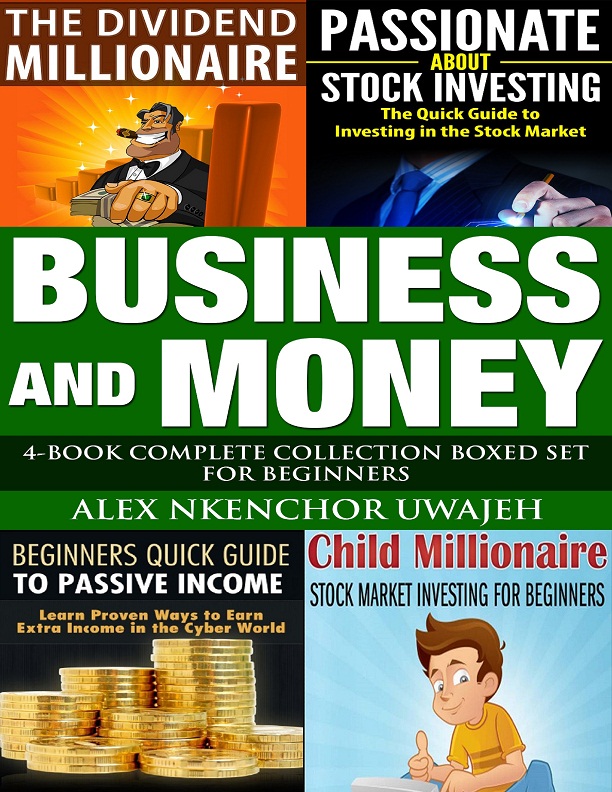
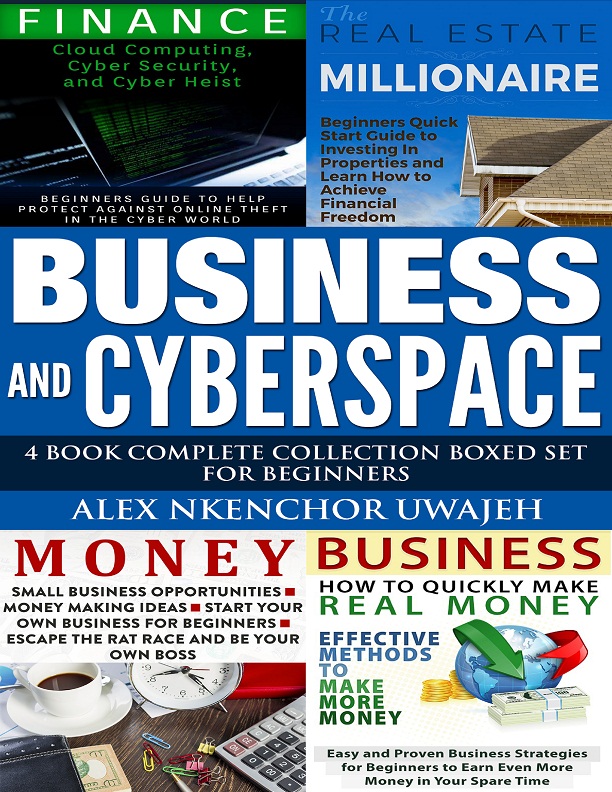
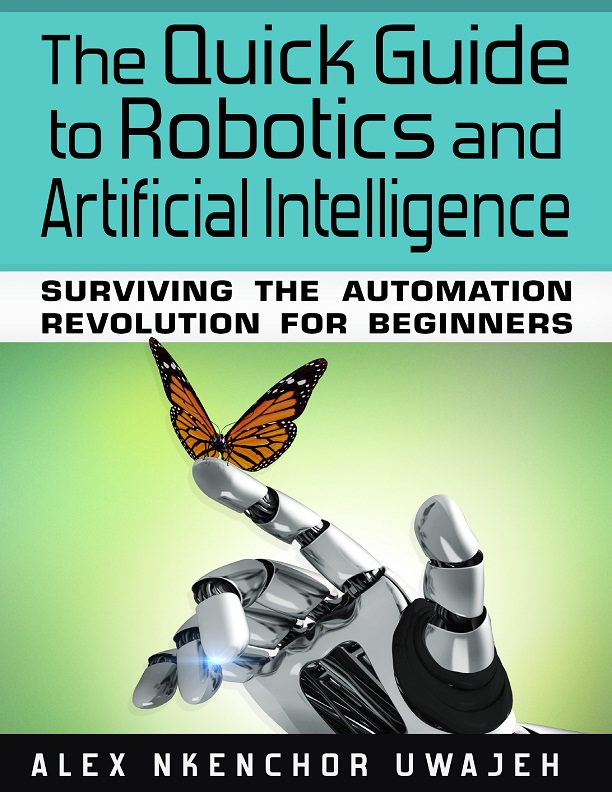
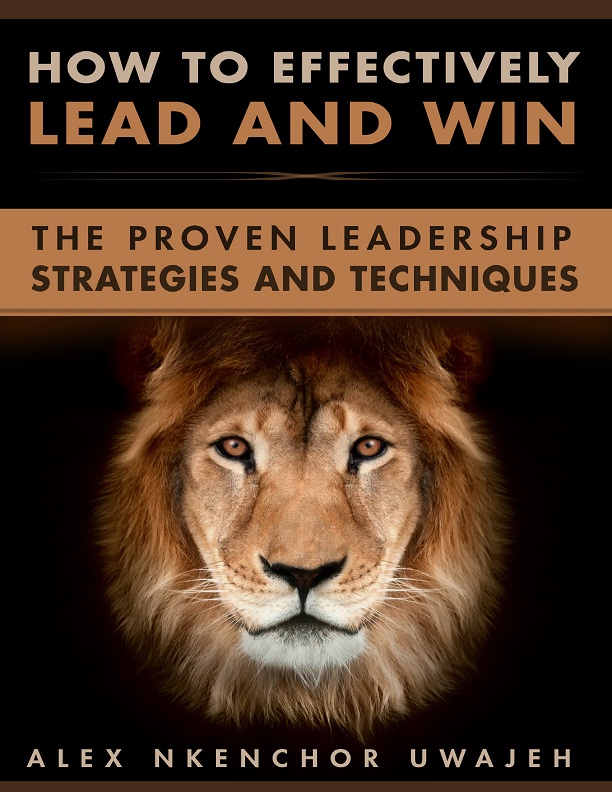
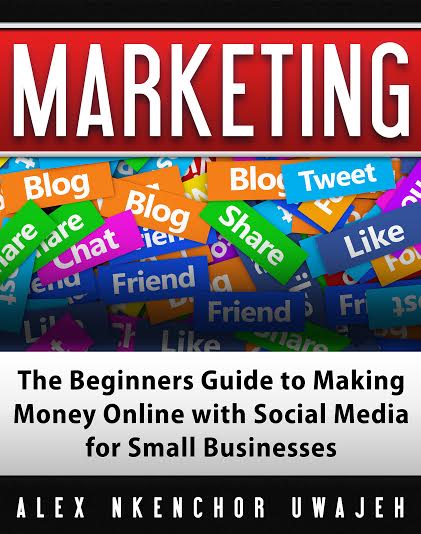
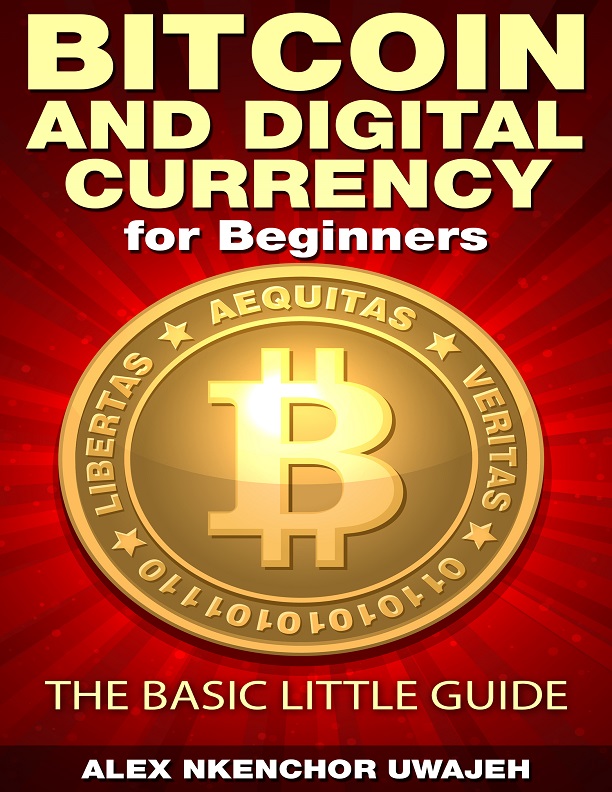
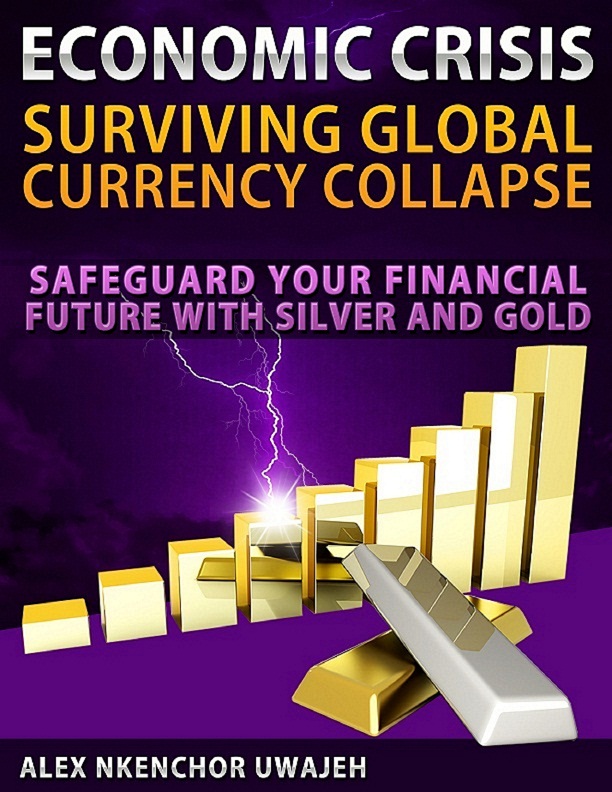
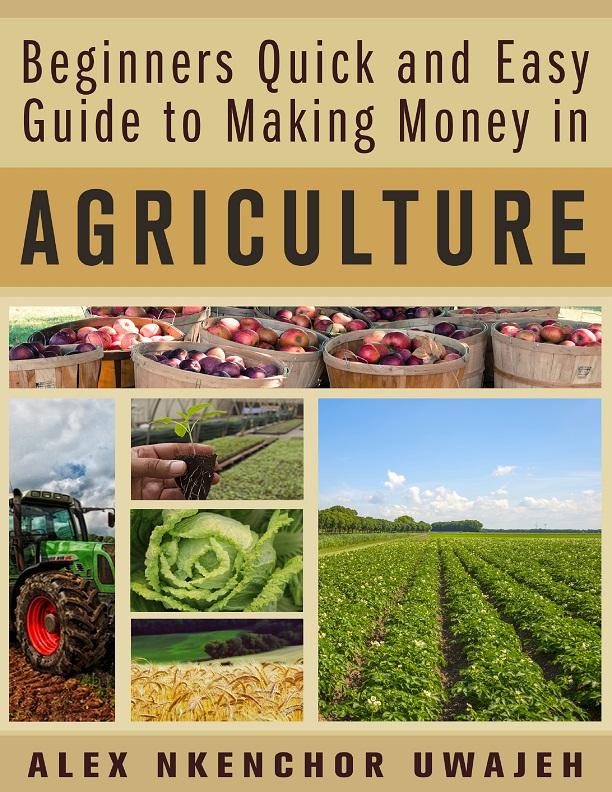
Browse
my Google Playstore Books
Buy
at Amazon
Want
Audible Audio Books? Start Listening Now, 30 Days Free
Return
to Home Page
|
|