Eco-friendly Toothpaste Manufacturing Process
Chapter 1: Introduction to Toothpaste Manufacturing
Overview of toothpaste and its importance in oral hygiene
Introduction to the toothpaste manufacturing process
Chapter 2: Raw Materials Used in Toothpaste Manufacturing
Common ingredients used in toothpaste production
Explanation of their functions and benefits in oral care
Chapter 3: Preparing the Water Phase
Purification of water for toothpaste manufacturing
Addition of humectants, flavorings, and preservatives
Chapter 4: Mixing the Water Phase
Introduction to the mixing equipment used in toothpaste manufacturing
Blending of water with additives and humectants
Chapter 5: Preparation of the Oil Phase
Introduction to oil-based ingredients used in toothpaste
Melting, heating, and blending of oils and waxes
Chapter 6: Combining the Water and Oil Phases
Emulsification process for combining water and oil phases
Formation of a stable toothpaste base
Chapter 7: Incorporating Abrasives
Introduction to abrasive materials used in toothpaste
Mixing and adding abrasives to the toothpaste base
Chapter 8: Adding Active Ingredients
Overview of active ingredients such as fluoride, desensitizing agents, etc.
Incorporating active ingredients into the toothpaste mixture
Chapter 9: Coloring and Flavoring
Introduction to coloring agents used in toothpaste
Addition of flavors and sweeteners for taste enhancement
Chapter 10: Adjusting Consistency and Viscosity
Techniques for controlling toothpaste thickness and consistency
Addition of thickening agents and viscosity modifiers
Chapter 11: Quality Control in Toothpaste Manufacturing
Importance of quality control measures
Testing toothpaste for various parameters such as pH, fluoride content, etc.
Chapter 12: Filling and Packaging
Introduction to toothpaste tube filling machines
Packaging options for toothpaste and their advantages
Chapter 13: Tube Sealing and Coding
Sealing techniques for toothpaste tubes
Coding and labeling of toothpaste tubes
Chapter 14: Tube Printing and Inspection
Printing methods for adding batch numbers, expiration dates, etc.
Inspection of tubes for quality assurance
Chapter 15: Case Packing and Shipment
Packaging toothpaste tubes into larger cases
Shipping and distribution of finished toothpaste products
Chapter 16: Toothpaste Manufacturing Automation
Overview of automated processes in toothpaste manufacturing
Advantages and challenges of automation in the industry
Chapter 17: Environmental Considerations
Discussion on eco-friendly toothpaste manufacturing practices
Recycling and waste management in toothpaste production
Chapter 18: Safety Measures in Toothpaste Manufacturing
Importance of safety protocols in the production facility
Handling of chemicals and equipment safety precautions
Chapter 19: Regulatory Compliance in Toothpaste Manufacturing
Overview of regulations governing toothpaste production
Ensuring compliance with local and international standards
Chapter 20: Trends and Innovations in Toothpaste Manufacturing
Introduction to the latest trends and innovations in the industry
New ingredients, packaging, and formulations
Chapter 21: Customized and Specialty Toothpastes
Manufacturing process for specialized toothpaste variants
Production of toothpaste for sensitive teeth, whitening, etc.
Chapter 22: Quality Assurance and Shelf Life
Shelf life testing and determination
Ensuring product quality throughout the entire shelf life
Chapter 23: Global Toothpaste Manufacturing Landscape
Overview of toothpaste manufacturing on a global scale
Major players and market trends in different regions
Chapter 24: Challenges and Future Prospects
Discussing the challenges faced by toothpaste manufacturers
Potential future developments and opportunities in the industry
Chapter 25: Conclusion
Recap of the toothpaste manufacturing process
Final thoughts on the significance of manufacturing toothpaste for oral care.
Chapter 1: Introduction to Toothpaste Manufacturing
Toothpaste is a vital component of oral hygiene, playing a crucial role in maintaining dental health. It is a gel or paste that is used in conjunction with a toothbrush to clean and protect the teeth and gums. Toothpaste manufacturing involves a series of processes that result in the final product we find on store shelves.
The manufacturing process begins with the formulation of the toothpaste. The formulation is based on a combination of active ingredients, such as fluoride for cavity prevention, desensitizing agents for tooth sensitivity relief, and antimicrobial agents for fighting bacteria. Other key ingredients include abrasives, which aid in the removal of plaque and stains, and humectants, which retain moisture and prevent the toothpaste from drying out.
Chapter 2: Raw Materials Used in Toothpaste Manufacturing
Toothpaste production relies on a range of raw materials, each serving a specific purpose. These include:
Water: Purified water is a fundamental ingredient used in toothpaste manufacturing. It undergoes purification processes to remove impurities and ensure its quality.
Humectants: These ingredients, such as glycerin or sorbitol, help maintain moisture in the toothpaste, preventing it from drying out.
Binders: Binders, such as carboxymethyl cellulose (CMC), give toothpaste its characteristic consistency and texture.
Surfactants: Surfactants, such as sodium lauryl sulfate (SLS), enable the toothpaste to foam and spread evenly during brushing.
Abrasives: Abrasive materials, such as calcium carbonate or hydrated silica, help remove plaque, stains, and food particles from the teeth.
Fluoride: Fluoride is a key ingredient for cavity prevention. Sodium fluoride, stannous fluoride, or sodium monofluorophosphate are commonly used.
Flavorings and sweeteners: These ingredients enhance the taste of toothpaste and make it more enjoyable to use. Common flavors include mint, spearmint, and fruit flavors.
Chapter 3: Preparing the Water Phase
The water phase preparation involves purifying the water and adding various additives and ingredients. The purification process ensures that the water used in toothpaste manufacturing meets strict quality standards. Filtration, distillation, and deionization processes are commonly employed to remove impurities, microbes, and chemicals.
To enhance the toothpaste's performance, humectants like glycerin or sorbitol are added during this phase. These humectants help prevent the toothpaste from drying out, maintain its consistency, and improve its overall shelf life.
Additionally, flavorings and sweeteners may be incorporated during this phase to impart the desired taste and freshness to the toothpaste. Common flavoring agents include essential oils, such as peppermint or spearmint, while sweeteners like saccharin or xylitol add a hint of sweetness.
Preservatives may also be added to inhibit microbial growth and maintain the product's integrity throughout its shelf life. Common preservatives include sodium benzoate or parabens.
Chapter 4: Mixing the Water Phase
Once the water has been prepared and the additives have been added, the next step is to mix the water phase. This involves the use of mixing equipment, such as agitators or blenders, to ensure thorough blending and homogeneity of the water and its additives.
The mixing process is crucial to achieve a uniform distribution of ingredients, ensuring that the final toothpaste product is consistent in quality and performance. The speed and duration of mixing are carefully controlled to achieve the desired results.
Chapter 5: Preparation of the Oil Phase
In addition to the water phase, toothpaste formulations often include an oil phase. The oil phase typically consists of oils, waxes, and other lipid-based ingredients. These ingredients serve several purposes, including lubrication, moisturization, and stability enhancement.
The oil phase ingredients, such as mineral oil, vegetable oils, or petrolatum, are heated and melted to achieve a liquid state. This ensures easy blending with the other toothpaste components during subsequent manufacturing steps.
Waxes, such as beeswax or candelilla wax, may also be added to the oil phase. These waxes contribute to the toothpaste's consistency, texture, and stability.
Chapter 6: Combining the Water and Oil Phases
Once the water phase and oil phase are prepared, they are combined to create a stable toothpaste base. This process, known as emulsification, involves blending the water and oil phases together.
Emulsification is typically achieved using specialized equipment, such as high-speed mixers or homogenizers. These machines apply shear forces to break down the oil droplets and disperse them uniformly in the water phase, creating a stable emulsion.
Emulsifiers, such as lecithin or sorbitan esters, may be added during this step to facilitate the formation and stabilization of the emulsion. These emulsifiers help to prevent phase separation and maintain the toothpaste's uniform consistency.
Chapter 7: Incorporating Abrasives
Abrasives are essential components of toothpaste as they assist in the mechanical removal of plaque, stains, and food particles from the teeth. Abrasives are typically mineral-based substances, such as calcium carbonate, silica, or alumina.
During the manufacturing process, the abrasives are added to the toothpaste base in a controlled manner. The mixing equipment ensures the even distribution of abrasives throughout the toothpaste, allowing for effective cleaning without damaging the tooth enamel.
The amount of abrasive used in toothpaste varies depending on the desired level of cleaning and the target market. Different toothpaste variants, such as those for sensitive teeth or whitening purposes, may contain different types or levels of abrasives.
Chapter 8: Adding Active Ingredients
Active ingredients in toothpaste provide specific oral health benefits. These ingredients may include fluoride for cavity prevention, desensitizing agents for tooth sensitivity relief, and antimicrobial agents for combating bacteria and gum diseases.
During the manufacturing process, the active ingredients are carefully incorporated into the toothpaste base. The addition is done gradually, ensuring uniform dispersion throughout the product.
For fluoride-containing toothpaste, the fluoride compound, such as sodium fluoride or stannous fluoride, is added in the required concentration. Desensitizing agents, like potassium nitrate or strontium chloride, are added to address tooth sensitivity issues. Antimicrobial agents, such as triclosan or zinc citrate, may also be included to help fight plaque and gum diseases.
Chapter 9: Coloring and Flavoring
Coloring agents and flavors are added to toothpaste to enhance its appeal and make it more enjoyable to use. Coloring agents are typically food-grade dyes or pigments that are safe for oral use.
Toothpaste flavors are carefully selected to provide a pleasant taste and fresh breath sensation. Common flavors include mint (peppermint or spearmint), fruit flavors, or herbal flavors. The flavoring agents used can be natural extracts, synthetic compounds, or a combination of both.
The addition of colors and flavors is done in controlled amounts to achieve the desired sensory experience. It is important to note that the colorants and flavors used must comply with safety regulations and be compatible with the other ingredients in the toothpaste formulation.
Chapter 10: Adjusting Consistency and Viscosity
Toothpaste consistency and viscosity play a significant role in user experience. Some consumers prefer a thick toothpaste that stays on the toothbrush, while others prefer a thinner consistency that spreads easily.
To adjust the consistency and viscosity of the toothpaste, thickeners and viscosity modifiers are added. Common thickeners include cellulose derivatives (such as carboxymethyl cellulose or hydroxyethyl cellulose) or natural gums (such as xanthan gum or carrageenan). These thickeners increase the viscosity and provide a desired texture to the toothpaste.
The amount of thickener added depends on the desired consistency and the specific formulation requirements. Manufacturers carefully balance the thickness to ensure ease of dispensing and satisfactory user experience.
Chapter 11: Quality Control in Toothpaste Manufacturing
Quality control is a crucial aspect of toothpaste manufacturing to ensure that the final product meets established standards for safety, efficacy, and performance. Various quality control measures are implemented throughout the manufacturing process.
Samples from different stages of production are collected and tested for various parameters, including pH level, fluoride content, microbial load, viscosity, and abrasive particle size. These tests help confirm that the toothpaste meets the specified requirements and maintains consistent quality.
In addition to in-house testing, external quality control may also be performed by independent laboratories or regulatory bodies to ensure compliance with industry regulations and standards.
Chapter 12: Filling and Packaging
Once the toothpaste has undergone quality control checks, it is ready for filling and packaging. Tube filling machines are commonly used in toothpaste manufacturing. These machines fill the toothpaste into collapsible tubes, which are the most popular packaging format for toothpaste.
The filling process involves precise dosing of the toothpaste into the tubes to ensure accurate volume and weight. The filled tubes are then sealed to prevent leakage and maintain the integrity of the product.
Chapter 13: Tube Sealing and Coding
After the toothpaste tubes are filled, they undergo sealing to ensure product integrity and prevent contamination. Tube sealing methods include heat sealing, ultrasonic sealing, or crimping, depending on the type of tube and the specific sealing equipment used.
Additionally, coding and marking on the tubes are essential for product identification, traceability, and expiry date information. Batch numbers, manufacturing dates, and other relevant information are imprinted on the tubes during this stage.
Chapter 14: Tube Printing and Inspection
Tube printing involves the application of labels or printing directly on the tube surface. This process adds branding elements, product information, and regulatory markings to the toothpaste tubes.
The printed tubes then undergo a comprehensive inspection to ensure the quality and accuracy of the printing. Automated systems may be employed to detect any printing defects, such as smudging or incomplete markings.
Chapter 15: Case Packing and Shipment
Once the toothpaste tubes are filled, sealed, printed, and inspected, they are ready for case packing. The filled tubes are grouped and packed into larger cases or cartons for efficient storage, transportation, and distribution.
The case packing process involves arranging the toothpaste tubes in a predetermined pattern or configuration to optimize space utilization and protect the tubes from damage during transit.
After case packing, the toothpaste is prepared for shipment to distribution centers, retail stores, or other points of sale. Proper labeling and documentation are crucial for tracking and inventory management during the shipment process.
Chapter 16: Toothpaste Manufacturing Automation
Automation has become increasingly prevalent in toothpaste manufacturing, offering numerous benefits such as improved efficiency, precision, and consistency.
Automated systems and equipment are utilized for tasks such as ingredient dosing, mixing, emulsification, and filling. These systems ensure accurate measurements, reduce human error, and enhance productivity.
Advanced technologies, such as robotics and computerized control systems, enable precise control of the manufacturing process. They also facilitate real-time monitoring and data collection for quality control and process optimization.
However, while automation offers many advantages, it also requires careful oversight, maintenance, and skilled personnel to ensure smooth operation and address any technical issues that may arise.
Chapter 17: Environmental Considerations
Toothpaste manufacturers are increasingly prioritizing environmental sustainability in their operations. Several initiatives and practices contribute to reducing the industry's environmental footprint.
Sustainable sourcing of raw materials, such as responsibly harvested plant-based ingredients or recycled packaging materials, is becoming more common. Manufacturers are also implementing eco-friendly production processes that minimize energy and water consumption, as well as waste generation.
Recycling and waste management programs are integral to toothpaste manufacturing. Efforts are made to recycle packaging materials and reduce the use of non-recyclable components. Proper disposal of manufacturing waste and adherence to environmental regulations are essential to minimize the environmental impact of toothpaste production.
Chapter 18: Safety Measures in Toothpaste Manufacturing
Toothpaste manufacturing involves handling chemicals, equipment, and potential hazards. Therefore, safety measures are of paramount importance to protect the workers and ensure a safe manufacturing environment.
Manufacturers adhere to strict safety protocols, including training employees on proper handling procedures, using personal protective equipment (PPE), and maintaining a clean and organized workspace. Regular equipment maintenance and safety inspections are conducted to identify and address any potential risks.
Chemical storage areas are designed to meet safety standards, and hazardous materials are handled and disposed of in compliance with local regulations. Additionally, manufacturers stay updated with safety guidelines and best practices to continuously improve safety measures.
Chapter 19: Regulatory Compliance in Toothpaste Manufacturing
Toothpaste manufacturing is subject to various regulations to ensure product safety, quality, and efficacy. Regulatory compliance involves adherence to local and international standards set by regulatory bodies such as the Food and Drug Administration (FDA) or the European Medicines Agency (EMA).
Manufacturers must comply with regulations related to ingredient safety, labeling requirements, product claims, and manufacturing practices. Rigorous testing, documentation, and quality control measures are implemented to meet these regulations.
To ensure compliance, manufacturers often collaborate with regulatory experts, conduct internal audits, and stay updated with the latest regulatory changes. Non-compliance can result in penalties, recalls, or restrictions on product distribution.
Chapter 20: Trends and Innovations in Toothpaste Manufacturing
The toothpaste manufacturing industry continuously evolves to meet consumer demands and incorporate technological advancements. Several trends and innovations have emerged in recent years:
Natural and organic toothpaste: Increasing consumer interest in natural and organic products has led to the development of toothpaste formulations with plant-based ingredients, free from artificial additives or harsh chemicals.
Specialty toothpaste variants: Manufacturers are creating toothpaste formulations tailored for specific oral care needs, such as tooth sensitivity, whitening, gum health, or children's oral care. These specialized variants often contain unique combinations of active ingredients and flavors.
Novel packaging designs: Manufacturers are exploring innovative packaging options, such as sustainable materials, easy-to-use dispensers, or travel-friendly formats, to enhance convenience and reduce environmental impact.
Smart toothpaste: The integration of technology into oral care has given rise to smart toothpaste solutions. These toothpaste formulations may include features like built-in sensors, antimicrobial properties, or interactive capabilities for personalized oral care routines.
Research-backed formulations: With advancements in oral health research, manufacturers are incorporating scientific findings into toothpaste formulations. This includes the use of new active ingredients, delivery systems, and formulation techniques to enhance effectiveness.
Chapter 21: Customized and Specialty Toothpastes
To cater to diverse consumer preferences and oral health needs, manufacturers produce customized and specialty toothpaste variants. These variants target specific concerns or requirements, offering unique formulations and benefits.
For individuals with sensitive teeth, desensitizing toothpaste is formulated with ingredients like potassium nitrate or strontium chloride to provide relief from tooth sensitivity. Whitening toothpaste contains gentle abrasives or hydrogen peroxide to help remove stains and brighten teeth.
Toothpaste for children is designed with milder flavors, lower fluoride concentrations, and age-appropriate packaging to encourage proper oral hygiene habits. Herbal or natural toothpaste variants use plant-based ingredients and exclude artificial additives, appealing to consumers seeking more natural options.
Manufacturers develop these customized toothpaste formulations by carefully selecting specific ingredients and adjusting concentrations to address targeted oral health concerns effectively.
Chapter 22: Quality Assurance and Shelf Life
Ensuring product quality and determining the shelf life of toothpaste are crucial aspects of the manufacturing process.
Quality assurance involves rigorous testing of the toothpaste at various stages, including raw materials, in-process samples, and finished products. Tests assess key parameters such as pH level, fluoride content, abrasiveness, microbial load, viscosity, and stability.
To determine shelf life, manufacturers conduct stability studies, subjecting toothpaste samples to accelerated aging conditions. These studies simulate the product's exposure to different environmental factors, such as temperature, light, and humidity. By monitoring changes in key quality attributes over time, manufacturers can establish an accurate expiration date for the product.
Chapter 23: Global Toothpaste Manufacturing Landscape
Toothpaste manufacturing is a global industry with numerous manufacturers operating on regional and international scales. Several key players dominate the market, producing toothpaste brands that cater to diverse consumer preferences.
Different regions have their market dynamics, influenced by factors such as consumer behavior, oral health awareness, regulatory frameworks, and cultural preferences. The toothpaste manufacturing landscape is characterized by intense competition, continuous product innovation, and the adoption of sustainable practices.
Emerging markets, such as Asia-Pacific and Latin America, offer significant growth opportunities due to rising disposable incomes, increasing oral health awareness, and expanding consumer markets.
Chapter 24: Challenges and Future Prospects
The toothpaste manufacturing industry faces various challenges and opportunities for future growth and development:
Raw material availability and costs: Ensuring a consistent supply of high-quality raw materials at competitive prices can be a challenge due to factors such as market volatility, environmental concerns, and geopolitical factors. Manufacturers need to develop strategic sourcing plans to mitigate these challenges.
Sustainability and eco-friendly practices: Consumers are increasingly demanding sustainable and environmentally friendly products. Toothpaste manufacturers need to focus on sustainable sourcing, reducing packaging waste, and implementing energy-efficient manufacturing processes to align with these expectations.
Technological advancements: Rapid advancements in technology, such as automation, artificial intelligence, and data analytics, offer opportunities for optimizing production processes, improving quality control, and enhancing product innovation.
Regulatory compliance: Staying compliant with evolving regulations and ensuring adherence to safety standards remains a continuous challenge for toothpaste manufacturers. Close collaboration with regulatory authorities and staying updated with the latest requirements are crucial to navigate this landscape.
Consumer preferences and market trends: Understanding changing consumer preferences, such as the demand for natural ingredients, personalized oral care, and innovative packaging, is vital for manufacturers to stay competitive and capture market share.
Chapter 25: Conclusion
The manufacturing process for toothpaste involves careful formulation, precise ingredient selection, and adherence to quality control measures. From preparing the water and oil phases to incorporating active ingredients, abrasives, colors, and flavors, manufacturers follow a systematic approach to create a safe and effective oral care product.
Toothpaste manufacturing continues to evolve with the introduction of new ingredients, packaging innovations, and sustainable practices. By staying abreast of consumer trends, technological advancements, and regulatory requirements, manufacturers can meet the changing demands of the market while prioritizing product safety, efficacy, and environmental sustainability.
Featured books
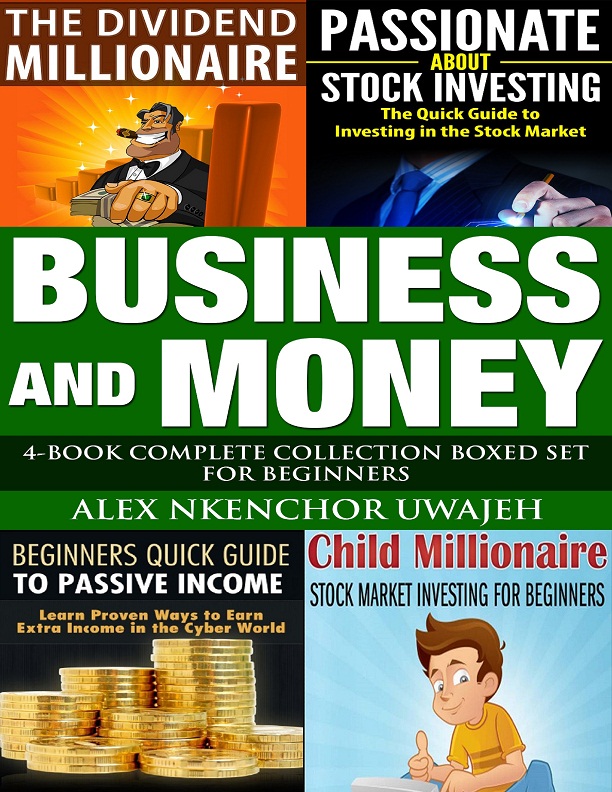
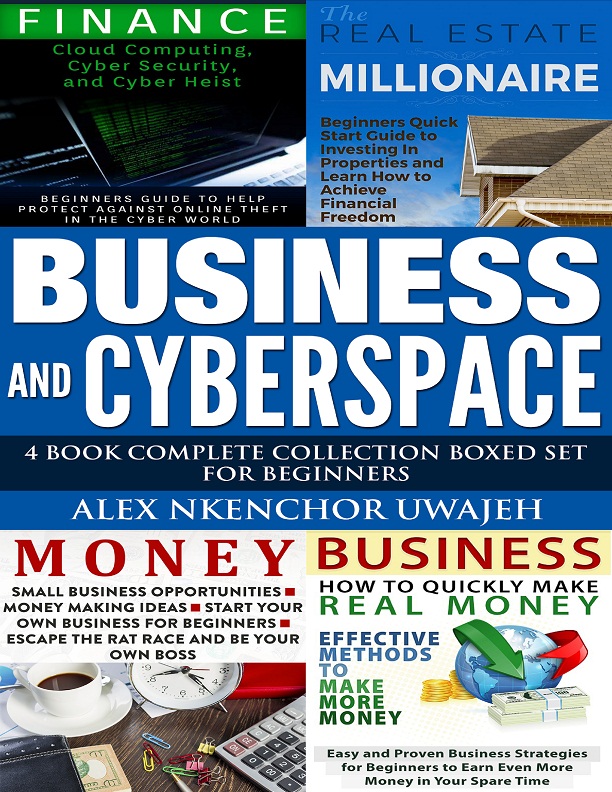
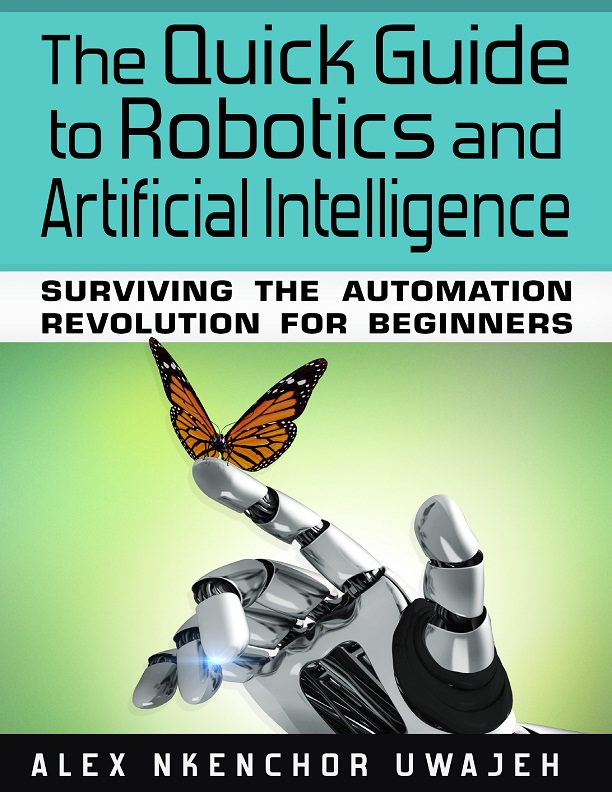
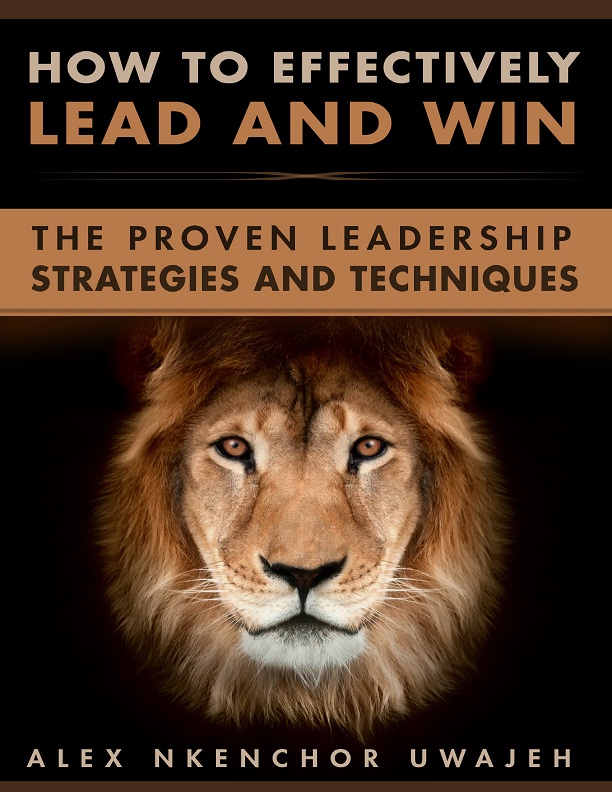
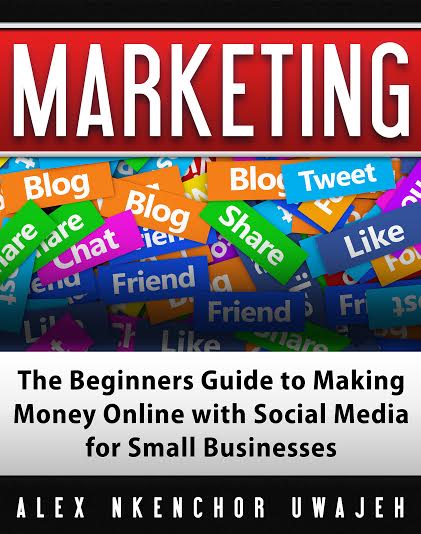
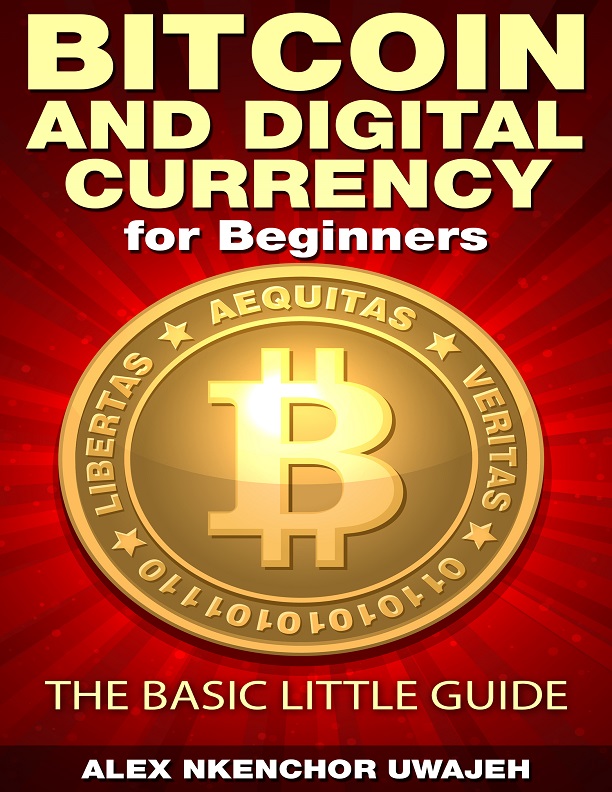
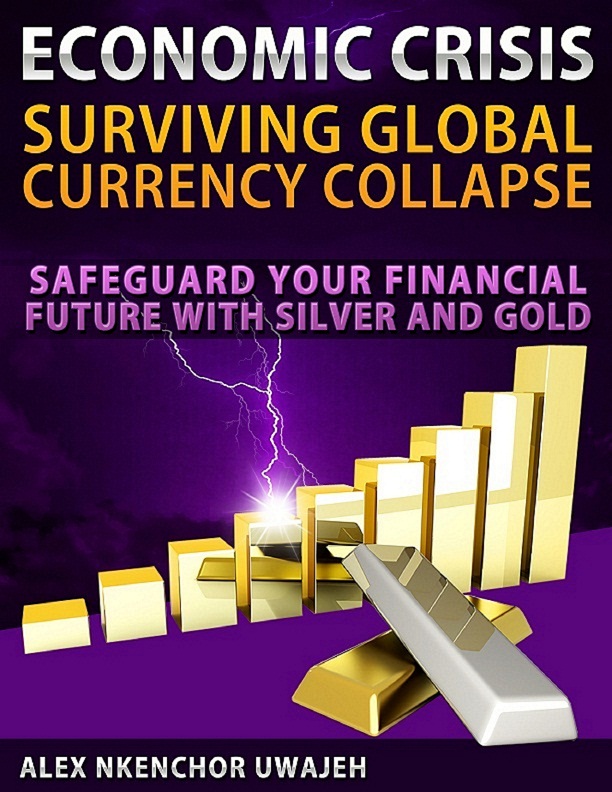
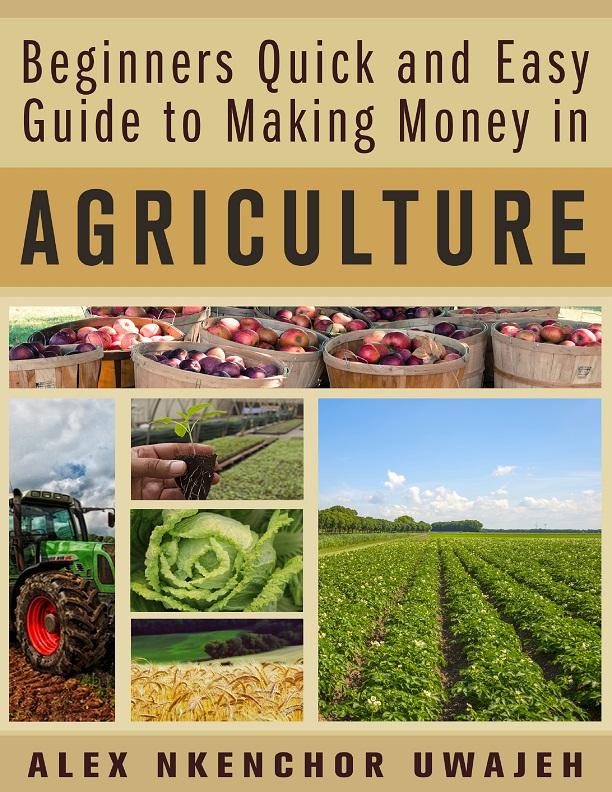
Browse
my Google Playstore Books
Buy
at Amazon
Want
Audible Audio Books? Start Listening Now, 30 Days Free
Return
to Home Page
|